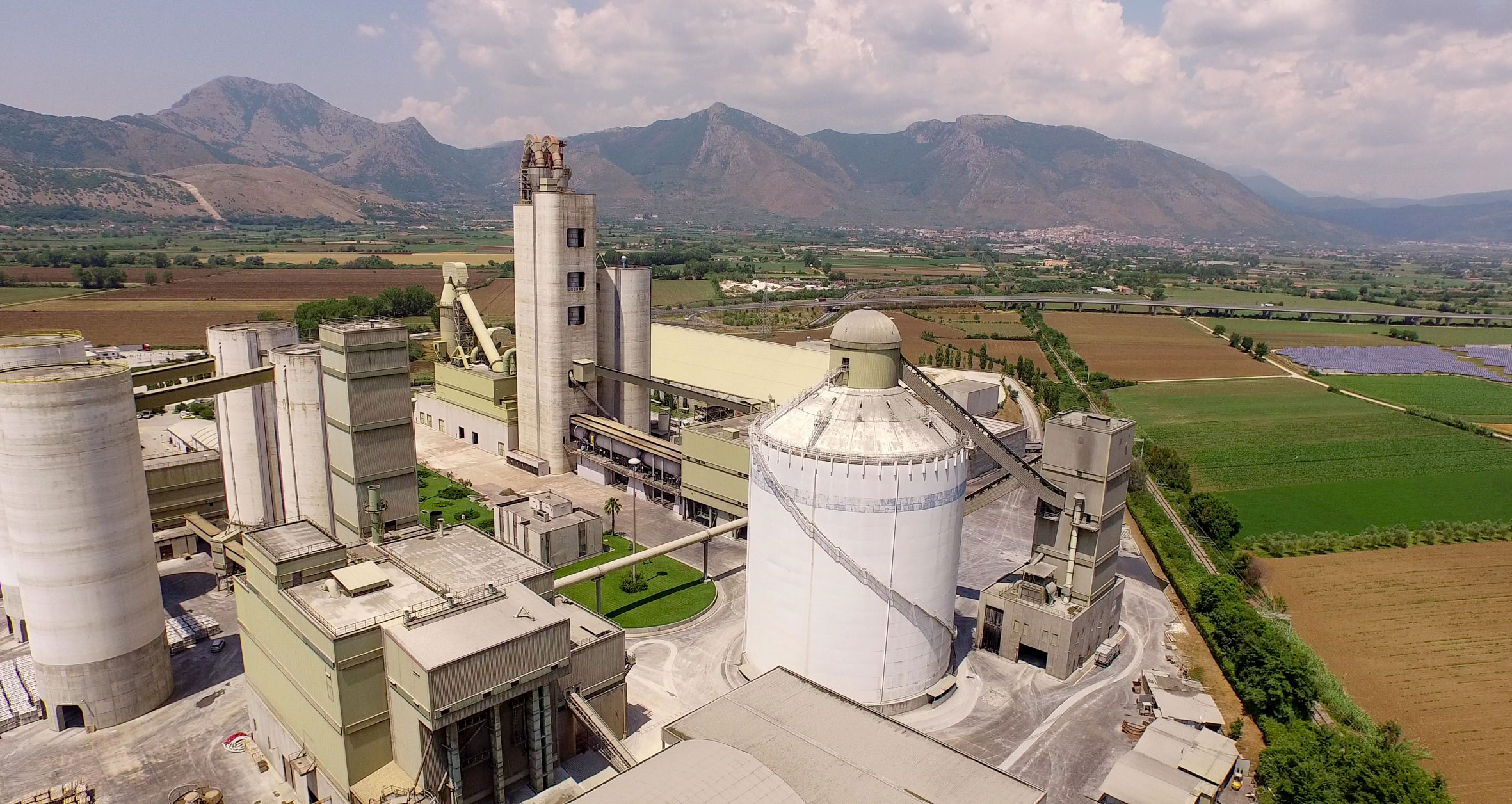
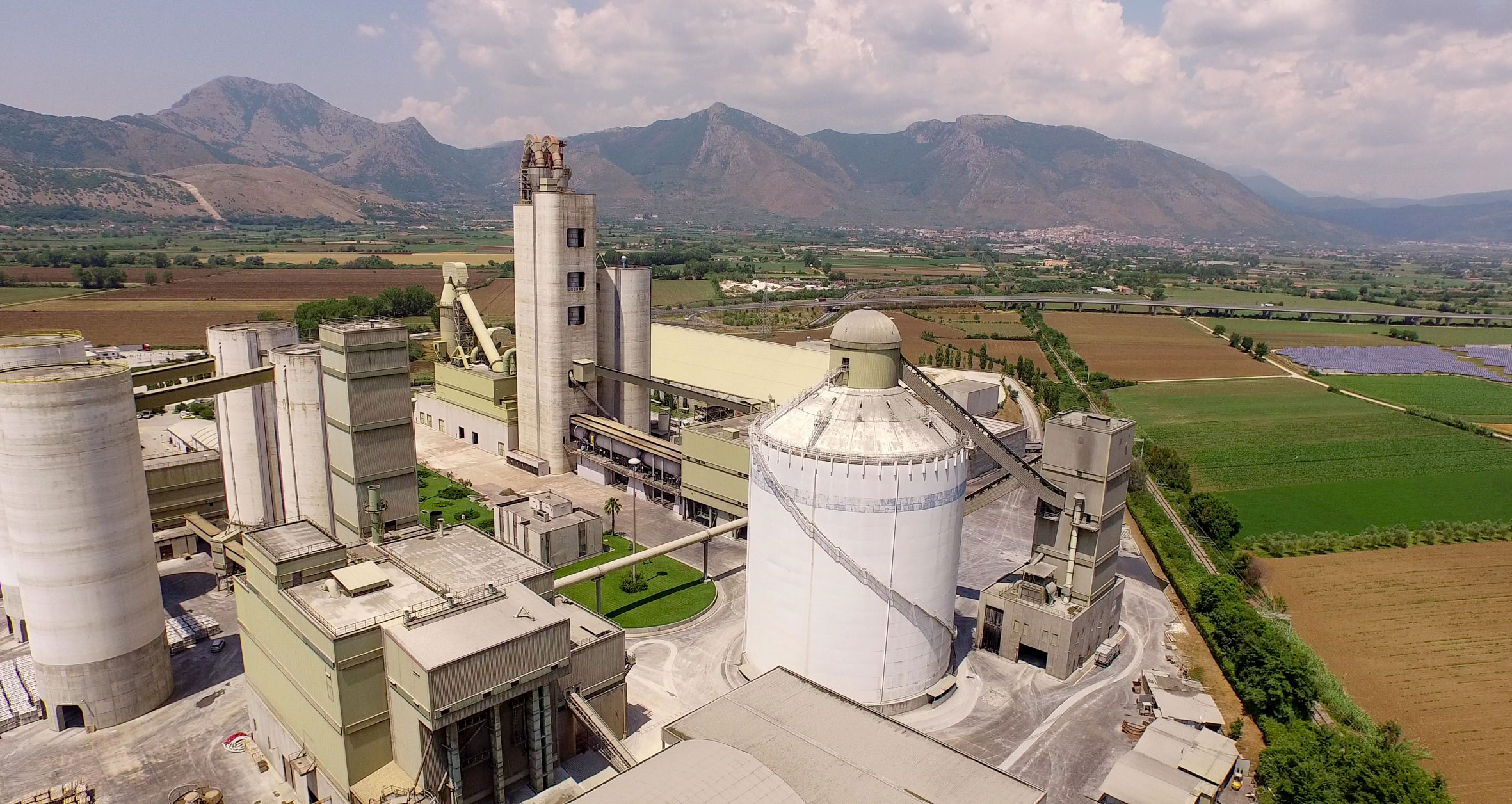
Die sogenannten „Hard-to-abate“-Sektoren (wortwörtlich „schwer zu mindern“) sind energieintensive Bereiche, in denen der Dekarbonisierungsprozess – d. h. die Reduzierung des Verbrauchs von fossilen Quellen mit daraus folgender Minderung der in die Atmosphäre freigesetzten CO2-Emissionen – am schwierigsten ist.
Dazu gehören u. a. die Sektoren Stahl, Chemie, Keramik, Glas und Zement. In diesem letzten Bereich ist auch die Colacem S.p.A. tätig, einer der Hautpakteure auf dem italienischen Markt, bei der ökologische Nachhaltigkeit seit jeher großgeschrieben wird, und die sich mit der Technologie Sybil ausgestattet hat, um ihre Produktion zu optimieren.
Zement ist das am meisten verwendete Material in der Bauindustrie, und aus diesem Grund ist seine Herstellung sehr wichtig für die Wirtschaft und die Entwicklung unserer Städte. Der Prozess, der zu seiner Herstellung führt, ist sehr energie- und emissionsintensiv und zwingt die Unternehmen, die ihn herstellen, in allen Phasen der Produktentwicklung auf höchste Effizienz zu achten. Colacem S.p.A. ist ein hervorragendes Beispiel dafür, wie dieser Prozess sehr gut gemanagt werden kann.
Die Technologie, von der hier berichtet wird, wurde von Alperia im Werk Sesto Campano (Isernia) entwickelt, das vor Kurzem die Umweltzertifizierung nach UNI EN ISO 14001 erhalten hat, was den nachhaltigen Ansatz von Colacem zugunsten des lokalen Gebiets und der dort lebenden Gemeinschaft bestätigt.
Das wichtigste Material bei der Herstellung von Zement ist Klinker. Dies ist die Grundmasse, die mit Gips und anderen Bestandteilen zerkleinert wird, um den Zement zu bilden.
Das durch das Mahlen von Rohstoffen (z. B. Mergel, Kalkstein, Lehm) gewonnene Mehl wird in einem Ofen bei sehr hohen Temperaturen gebrannt und chemisch und physikalisch in Klinker umgewandelt. Die Feuerungsanlage besteht aus drei Teilen, die nacheinander arbeiten: Wärmetauscherturm, Drehrohrofen und Kühlrost.
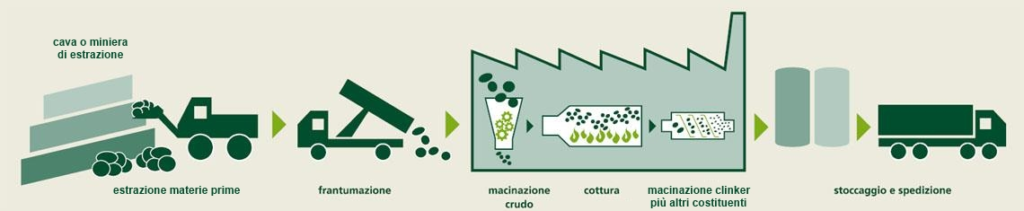
Alperia Sybil Industrial, das von Alperia entwickelte fortschrittliche Steuerungssystem, kommt genau in den letzten beiden Bereichen der Backanlage zum Einsatz und ist in der Lage, komplexe industrielle Prozesse zu optimieren.
Im Inneren des Drehrohrofens reduziert Alperia Sybil Industrial den Verbrauch von Petrolkoks (Erdölkoks), dem Hauptbrennstoff in der Feuerungsphase, ohne Beeinträchtigung der Produktionskapazität, während es in der Abkühlungsphase die Regelung der Rostventilatoren optimiert und damit einen doppelten Nutzen erzielt: zum einen die Steigerung der Effizienz der Verbrennung im Ofen und zum anderen die Reduzierung des Stromverbrauchs.
Die in den ersten beiden Betriebsjahren erzielten Vorteile sind sowohl wirtschaftlicher als auch ökologischer Art: Die Petrolkokseinsparung beträgt im Vergleich zu den Bedingungen vor den Maßnahmen etwa 2.000 Tonnen pro Jahr, was einer Verringerung des Primärenergiebedarfs um etwa 1.500 t RÖE und damit einer Vermeidung von 6.800 Tonnen CO2e-Emissionen entspricht. Die Stromeinsparung durch den optimierten Betrieb des Kühlrosts liegt in der Größenordnung von 370 MWh pro Jahr (etwa 10 %) und entspricht rund 150 Tonnen vermiedenen CO2e-Emissionen.
Alperia Sybil Industrial basiert auf modellprädiktiven Kontrollstrategien (Model Predictive Control [1]), die in der Lage sind, Prozessschwankungen zu antizipieren und Korrekturmaßnahmen umzusetzen, um wichtige Variablen nahe an effizienten Werten zu halten.
„Technologische Innovation und Nachhaltigkeit gehören zu den wichtigsten Faktoren, die unsere Entwicklungsstrategien vorantreiben“, kommentiert Nando Tinti, Energy Manager der Colacem Gruppe. „Wir kennen die Erfahrung von Alperia bei der Entwicklung dieser Kontrollsysteme und daher war die Zusammenarbeit von Anfang an für beide Unternehmen fruchtbar. Das beweist der so genannte „Nutzungsfaktor“ des Systems, d. h. die Zeit, in der Alperia Sybil Industrial den Prozess optimiert, die über 90 % der Produktionszeit liegt.“